Introduction: Make Your Idea Real
This instructable will give you a better understanding on how to make something virtual (an idea, sketch, CAD model, etc.) into a real, physical object. Luckily, I work in an R&D department with a great deal of my time spent towards creating physical objects from ideas. I also do it at home for personal and business projects, so I will give you my insight on the topic.
There are many ways to go about creating a physical object from an idea. Depending on the object’s purpose, the choices usually narrow down pretty easily. I will list some of the main options we have, and what they are good for.
If the object you have in mind won’t take too much stress, rapid prototyping with polymers is the way to go, and it’s usually the most common form of bringing an idea to life.
FUSED DEPOSITION:
At work, we usually use an Objet 30 printer for most of our prototyping; this is a UV curable resin deposition printer. It basically has a head very similar to your everyday household inkjet, but deposits resin instead. The tray it deposits the resin on moves down as each layer (pass of the heads) gets piled on top of the last layer and a UV light attached to the heads cures the resin to a certain degree with every pass.
The results are pretty amazing as far as accuracy, and the material properties are good enough for general testing/use. We use them for general model representations, light/medium stress fixtures.
SLA:
Stereolithography is like a "pool" of resin that gets cured at the very top. A plate moves each consecutive cured layer deeper in the pool, and the top layer gets cured as well. This process continues and is in essence a type of extrusion of cured resin.
The results are good, not as close as fused deposition, but acceptable. The advantage of this method is a wider variety of materials that approximate physical properties of real polymers. We use them for working model prototypes.
SLS:
Selective laser sintering melts and bonds each powdered layer into shape. Much like the SLA principal, it extrudes the layers down.
The results are strong parts. The advantage of this method is that you may introduce a material fill/mix into your model, such as glass fibers, aluminum, carbon fibers, etc. We use these models for heavy fixtures.
URETHANE CAST:
You may choose this option if you’d like a larger quantity of objects. The initial cost for the mold is a bit more, but each consecutive part is far cheaper.
METAL FABRICATION:
Depending on your physical object requirements, it may be necessary to have a part CNC milled, sintered and finished (via SLS), or formed with metal material.
The resulting parts are very accurate, very strong, but very expensive. We only use this for large fixtures.
Step 1: Conceptualize Idea
We usually start off with a very rough sketch on paper with important dimensions. The purpose of this is to catch any obvious problems with your design before you start modeling it so you don’t waste time fixing something major while you are in the CAD process. Review the part for any changes which may occur once the part is installed, or once it’s functional (other things moving around it, interacting with it). If you are not familiar with the object’s physical behavior (if it’s important to you) as far as functionality and strength, you may want to have an engineer review it.
Step 2: Draw Parts
Now we make the object in CAD. There’s plenty of great CAD software available, and some of the top notch companies offer student versions of the software for a reasonable price. There are some free CAD programs available as well, but they may be much more time consuming to use.
If the CAD software has finite element analysis tools, you may want to check the structural integrity of the object.
If this is an object which will interact with other parts, it may be wise to model the other items as well and see how everything fits together in an assembly.
I have the privilege of working with SolidWorks, and I’m happy to say it’s probably my favorite CAD software.
Step 3: Prepare for Prototyping
Prepare the model for prototyping a physical object. This step includes some of the options listed above. If you were to send it out to a rapid prototyping, they would most likely ask you for a .STL or .STEP (214) file of your part. This is simply done by converting your file. If you choose the .STL format, you may want to check the quality of the converted output file. In SolidWorks, this is done by choosing options in the save dialog window, and editing accordingly. Something very important to remember is that in real life there are tolerances, and rapid prototyping will produce features with slightly different dimensions from the nominal (theoretical) size you have drawn your model with. You need to ask the company what their tolerances are and make changes to your model if needed before you send it out.
If you want to send it to a machine shop, you will have to make a detailed drawing, with all the necessary dimensions and tolerances (tolerances are very important and greatly contribute to the cost of machining your part).
Now, consider that I am at home and I don’t have too much money to spend on someone making a relatively simple part for me. What would I do? Well… enter wood! Wood is a great material for fabricating parts. It is readily available, easy to work with, fairly strong, and may be coated.
To begin making your part out of wood, let’s start with making a template to follow. This can be done by making a .pdf of the drawing (with the drawing views on a 1:1 scale, and make sure to at least center-mark any holes) and printing it out. I do this by making my drawing template an A4 and printing (with no special fit options) on a simple 8.5x11” paper.
Step 4: Trace Template
Cut out and trace the chosen view (this would be my top view). Tracing the parts is easier if you put a piece or two of masking tape on the corners of your cut view and the wood. Mark every hole center with a center punch or something similar. Trace with care and try not to crease or move the template as you trace it on the wood.
Step 5: Machine Features
Remove the template from the wood, and carefully cut your part out. It’s wise to drill holes first and cut the outline later, but sometimes the size of the object or machinery doesn’t permit this. Needless to say, you are doing this at your own risk so you need to be careful! Machines are dangerous, and one should have experience with any unfamiliar tool or machine prior to working on a project. I often make dummy parts just to test out a method first, so I have an idea of what to expect while making the actual part. You can always use multiple pieces to produce complex cavities and features.
Step 6: Finish Part
Once your part is produced, you may choose to coat it with a sealer to protect it. If you happen to need this part to be plastic, fear not, you can always cast it. Casting can be rather complicated, but in short words, you build an enclosure, use some sort of filler material if needed to make your parting line, make half the mold, then make the other half (including gates) and you are ready to produce a part. Simple in theory, but complicated to execute due to a need of several important working conditions. There's a lot of info on the web if you are interested.
Good luck creating your ideas, and remember to always be safe while working with tools or chemicals!
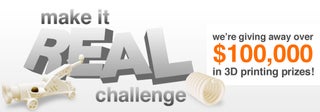
Participated in the
Make It Real Challenge