Introduction: Helical Shelf System
This furniture explores how 3D printing can unlock new possibilities in form, mechanisms and personal fabrication. The shelf system is comprised of triangular helices, cogs, belts and wooden shelves. The helices move together and cause the shelves to move up and down. This example has two different helices that are attached together. Geometrically they twist in opposite directions so when they are rotated one shelf rises and the other lowers. They have the same rotational frequency but have different heights so the shelves move to the full parameters of the height of the helices. The helices move through helical components that are screwed into the wooden shelf. The feet at the bottom are functional and sculptural, bracing the rods and housing each cog and belt. The helices and feet are great examples of the complex forms easily achievable with a cheap 3D printer.
The included parametric grasshopper file enables anyone to create their own variation of the helical shelf principle. The instructions included are for the version in the photos. This is at first prototype stage and initially I intended for a handle to cause the helices to rotate however there was too much friction so now I lift one of the shelves and this causes the kinetic change and the other shelf moves in the opposite direction. A clasp connects to a hole in the large cog and prevent the shelves from moving from a desired position.
Attachments
Step 1: Materials/ Printed Parts
You will need
ABS (FDM 3D Printer) download the STL files (also available on Thingiverse) and print (refer to image)
Pillar drill
Drill bits (d)40mm, 25mm, 6mm
Selection of files
Wrench
Screwdriver
A x 4
B x 4
C x 4
D x 4
E x 4
F x 1
G x 4
H x 4
I x 4
J x 1
K
L x 2
M x 1
I will refer to the Key of parts throughout these instructions.
Parts B,C,D,G,J,L need to be filed down for smooth motion.
You may need some washers between parts G and E and I have included various different handles (I used M) My example uses different cogs as well, but you do not need to.
I used plastic weld to glue the parts together (http://www.modelhobbies.co.uk/shop/57ml-plastic-weld-cement-p-26493.html)
Wood
3 x 250,600,18mm (refer to image)
W1 x 2
W2 x 1
Metal
4 x M6 threaded rod 760mm+
1 x M6 Bolt 60mm
20 M6 Nuts
Thin wood screws approx. 15mm, 26mm
I used the cheapest M6 threaded rod. I think galvanized would be a bit more sturdy.
Belt
I used imperial pitch, L Pitch Rubber Timing Belts, (http://www.beltingonline.com/l-pitch-rubber-timing-belts-4582)
I got it cut at 1524mm length 8mm height, glass fibre,
Attachments
Step 2: Printing, Drilling, Filing, Sanding
I first taped all three 600/250/18mm wooden shelves on top of each other and marked the location of the holes. I used a pillar drill and a 2mm drill bit to drill all the way through the three shelves so all holes line up. I then sanded the corners with a belt sander. After that I removed the masking tape and drilled approximately 3mm depth with a 40mm diameter drill bit using the guide holes. I then drilled about half way through the shelf with a 25mm drill bit and then turned it over and drilled through the other side (to avoid shattering the MDF surface) The diagram shows the location of two other holes in one of the shelves. The holes are situated half way down the shelf and 55mm and 90mm in. This is the bottom shelf.
Printing all the parts takes a long time. I used Skeinforge settings 30mm/s with a 0.2 infill solidity.
Glue the helices on top of each other. Part B are the helices for the short helix and C and D are the long helix. Glue parts together with the pin at one end, do not glue the different helices together yet! File the helices and the helical bearings until they are smooth and move easily together. This takes a fair bit of time and I would advise starting with a rough file and ending with sand paper to give a smooth finish. Filing the bearing component more will allow you to file the helices less.
Step 3: Assembly: Moving Shelves
Before inserting the helical bearing components, you may want to add a finish to the wooden shelves. I just used a couple of coats of MDF sealer.
Insert parts H x 4 into the shelf. Ensure that all four are oriented in the same direction and the helix runs easily through them, then drill holes using 2mm drill bit and screw bearing components into place.
Then do the same for the other shelf and parts I x 4. Orient the second set of components in the same direction as before.
Step 4: Assembly: Feet and Belt System
The feet brace the helix rods and house the cog and belt.
Insert M6 nuts into the cogs and rotation bearings (parts E and G) and assemble with the M6 threaded rod. Let a fair amount of the rod through the bottom of the shelf to find the correct position of the foot (part A). The foot should move easily along the rod, if it does not file the hole. Put the belt around the cog and insert the foot into position, mark/drill the screw holes and screw into position. Repeat this for the other feet.
Next, assemble the handle and cog/clasp system. the M6 bolt goes through the handle (part M) and through the hole 90mm in from the edge of the shelf. Part F is 'nut up' with another nut beneath it tightened as much as possible (able to move freely). As I said before, this is the first prototype and so far I have been unable to get the handle to work because of too much friction. Currently I turn the furniture by turning the handle cog and belt.
The hole 55mm in is for part J. Reinforce part J by inserting a screw into it. This part will likely need filing down to fit through the shelf and into the cog clasp holes.
After that, file down and find a good location for the belt bearing (part L). If you use the same belt as me then it does not need to be tight. Drill and secure into position with a screw.
Step 5: Assembly
Reassemble all parts ensuring that motion is easy and parts are as tight as possible. You may need to add washers in some places to avoid parts clamping to the shelves.
The order of assembly goes: M6 rod attaches to part G, through bottom shelf, attaches to cog (part E) 'nut down' tightened as much as possible, add extra M6 nut and tighten with wrench as tight as possible, put belt over the cog, attach foot, ensure motion is smooth. Repeat for each pole.
After this you can test if one shelf works by inserting a set of helices over the rods and into the pins. Put some M6 nuts on top to avoid them popping out and test whether one shelf works. Before applying the belt, ensure all helices are in same orientation.
Then use plastic weld to glue the helices together with pins at either end. Wait 15 minutes, then remove the helices from the rods and lower the relative shelf over the rods. Then put the helices back onto the rods and move them through the shelf and into the pin holes of part G. If this is not working well, loosen the belt and then re-apply it. Add M6 nuts to the top of the rod and tighten with a wrench. Once this one shelf is working well, move it to its bottom position and drop the second shelf on top. Add the clasp at your desired position!
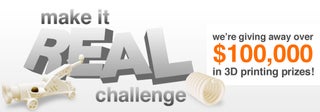
Participated in the
Make It Real Challenge